In the realm of innovative materials, conductive polyimide rods are emerging as a key innovation in design and engineering applications. Known for their remarkable thermal stability, chemical resistance, and mechanical strength, these high-quality polyimide rods are paving the way for innovations across various industries. As hsjuxin-pi continues to evolve, the ability to integrate conductivity into low-weight materials creates new avenues for engineers and designers alike, particularly in challenging fields such as space exploration.
The aerospace industry, in particular, is likely to reap substantial benefits from the unique properties of conductive polyimide rods. As aircraft and spacecraft turn increasingly complex, the need for materials that can endure extreme conditions while providing consistent electrical performance is crucial. By employing electrically-conductive polyimide rods, manufacturers can enhance both the functionality of their designs but also contribute to weight reduction, improving overall efficiency and performance in aerospace applications.
Advantages of Conductive Polyimide Rods
Conductive polyimide rods provide several key advantages to many industries, particularly due to their superior thermal stability and high performance. These rods can endure severe temperatures while preserving their structural integrity, making them suitable for applications in harsh environments. This characteristic is essential in fields such as aerospace, where materials are exposed to significant heat and stress. The ability to perform under such circumstances ensures dependability and safety in critical components.
Another significant advantage of conductive polyimide rods is their outstanding electrical conductivity. Unlike traditional insulative polyimides, the incorporation of conductive fillers enables these rods to conduct electrical signals efficiently. This characteristic opens new avenues for embedding electronic components into designs without compromising the benefits of polyimide, such as light profiles and chemical resistance. The aerospace industry, in particular, can leverage this advantage for innovative wiring solutions and sensor applications, enhancing overall performance.
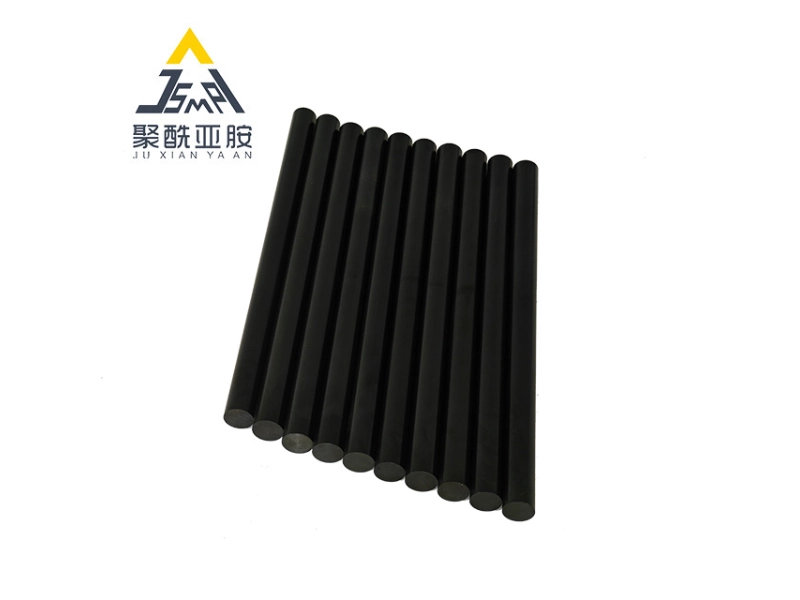
Additionally, conductive polyimide rods exhibit superior chemical resistance, which is essential for applications in settings where exposure to corrosive substances is common. This durability contributes to reduced maintenance costs and longer service life of components. As a result, industries that demand materials capable of enduring harsh chemical environments can benefit greatly from integrating these rods into their designs, resulting to improved efficiency and cost-effectiveness.
Applications in Aerospace Engineering
The aerospace industry requires substances that satisfy stringent operational standards while ensuring light and strength. Conductive polyimide rods are increasingly becoming a preferred choice because of their superior thermal stability and excellent mechanical properties. These rods can withstand extreme heat and radiation, which makes them suitable for multiple uses in aircraft and spacecraft design. This special combination of features allows engineers to create components that are strong yet lightweight, contributing to total fuel economy and performance.
Moreover, the conductive properties of conductive polyimide rods provides new avenues for incorporating sensors and electronic systems directly into structural components. This capability is vital for contemporary aerospace technologies that heavily depend on electronic monitoring and control. Through integrating these conductive rods within aircraft body designs, engineers can reduce weight and avoid the complications associated with traditional wiring, enhancing both design effectiveness and system reliability in aerial functions.
Finally, the flexibility of conductive polyimide rods allows for their application in prototype development and production. With the ability to be molded into complex shapes, these rods enable creative design solutions that meet the evolving needs of the aerospace sector. Their application ranges from reinforcing structures to specialized tooling, allowing for rapid development cycles and lowering market introduction time for emerging aerospace innovations. As the sector keeps to advance, the role of conductive polyimide rods will be key in introducing next-gen aerospace solutions.
Manufacturing Processes
A manufacturing of electrically conductive polyimide rods entails a series of sophisticated techniques designed to obtain high performance and precision. Initially, the process starts with the preparation of polyimide resin, which is usually synthesized through the polycondensation of a aromatic compound diamine and a aromatic compound dianhydride. This step is critical as it affects the thermal and electrical properties of the final product. The addition of conductive fillers, such as carbon black or metallic particles, improves electrical conductivity while preserving the desirable characteristics of polyimide.
Once the resin is prepared, the next step centers on shaping the rods. This is typically achieved through methods such as extrusion or injection molding. In extrusion, the molten resin is forced through a die to create long continuous rods, which are then chilled and cut to specified lengths. Injection molding, on the other hand, allows for complex geometries to be created by injecting the heated resin into a mold. Both processes demands precise temperature control and material handling to ensure quality and performance in the end product.
Following shaping, the rods undergo a curing process to develop the necessary mechanical and thermal stability. This involves heating the shaped polyimide in a regulated environment to facilitate cross-linking of the polymer chains. The curing temperature and duration vary based on the specific formulation of the resin and the target properties of the finished rods. After curing treatments may also be applied to boost the rods' durability and conductivity, tailoring them for specialized applications in industries such as aerospace.
Emerging Trends and Innovations
As the requirement for light and high-performance materials keeps increasing, polyimide conductive rods are positioned at the leading edge of development. The aviation industry, in specific, is anticipated to integrate these materials in greater depth in the upcoming years. With the emphasis on decreasing weight without compromising strength and performance, rods made from conductive polyimide provide an excellent solution for multiple applications, including structural components and electronic components within planes. Advancements in surface treatment and manufacturing processes are likely to further enhance the conductivity and physical attributes of these rods, making them even more suitable for strict aerospace standards.
A further area of potential growth is the integration of smart manufacturing techniques that leverage polyimide conductive rods in the production of cutting-edge electronic devices. As the IoT and intelligent technology keep evolving, the demand for materials that can easily combine with electronic sensors and other electronic components will spur progress in polyimide formulations. Recent advancements may feature improved thermal and electrical properties, which could open up possibilities for more miniaturized designs in electronic devices, automotive, and wearables.
R&D in body-safe conductive rods made of polyimide are also on the way, which could change the medical industry. These materials could be used for implants or intelligent medical tools that monitor physiological signals while being safe for extended use with body tissues. The persistent investigation of the chemistry of polyimides and working methods will certainly lead to advancements that introduce new uses in a wide range of industries, solidifying the position of polyimide conductive rods in upcoming design advancements.